caractéristique des isolant
Caractéristiques des isolants
Caractéristiques des
isolants : conductivité thermique, densité, perméabilité à la vapeur
d'eau.
Liste des isolants : laine de bois, polystyrène expansé, extrudé, polyuréthane, laines de verre ou de roche, chanvre, cellulose, perlite.
Liste des isolants : laine de bois, polystyrène expansé, extrudé, polyuréthane, laines de verre ou de roche, chanvre, cellulose, perlite.
On peut classer les matériaux isolants en
grands groupes :
- Les matériaux synthétiques (polystyrènes expansé et extrudé, polyuréthane, polyester) qui sont généralement efficaces en therme d'isolation mais non exempts de toxicité.
- Les fibres minérales, végétales et animales (laines de roche et laines de verres très répandues, mais aussi laines de bois, lin, chanvre, mouton, etc.).
- Les autres matériaux renouvelables (cellulose, liège, etc.).
- Les isolants minéraux, plus rarement utilisés (perlite, vermiculite, argile expansée, verre cellulaire).
- Les isolants minces réfléchissants.
Pour aller plus loin...
Les caractéristiques des isolants
Qualité
|
Effets recherchés
|
Type d'isolant à
éviter de ce point de vue (ne possédant pas cette qualité)
|
Faible
coefficient de conductivité thermique lambda
|
Freiner
l'échange de chaleur entre l'intérieur et l'extérieur.
|
-
Aujourd'hui, tous les matériaux isolants ont un bon lambda .
-
Par contre, les isolants minces, du fait de leur faible épaisseur, ont une
mauvaise résistance thermique.
|
-
Forte densité
-
Bonne aptitude à accumuler la chaleur
|
-
Amortir l'onde de variation de la température extérieure sur le cycle de 24
heures (pour rester au frais l'été)
-
Retarder la propagation du feu en cas d'incendie
-
Offrir une bonne isolation phonique.
|
Polystyrènes,
polyuréthane et laines de densité inférieure à 50 kg/m3
|
Perméabilité
à la vapeur d'eau
|
Permet
de laisser respirer la maison
|
Polystyrènes,
polyuréthane
|
Longévité
|
Absence
de tassement, pas d'apparition de "jours" aux raccords.
|
Laines
en rouleau ou en vrac
|
Absence
de nocivité
|
Pas
d'émanation toxique dûe à des additifs chimiques, pas de microfibres
irritantes.
|
Polystyrènes,
polyuréthane et dans une très moindre mesure laines minérales.
|
Isolation
préservée en cas d'humidité.
|
Efficacité
préservée de l'isolant par grand froid.
|
Aucun
matériau à éviter mais frein-vapeur obligatoire sur la face intérieure de
tous les isolants fibreux
|
La laine de bois
Les panneaux de laine de bois sont élaborés
à partir de fibres de bois, le liant étant la lignine de bois. Ce matériau
naturel est l'un des meilleurs isolants disponibles sur le marché :
- coefficient d'isolation identique aux autres laines isolantes ;
- structure rigide à assemblage rainuré garantissant une très grande longévité ;
- nombreux produits spécialement adaptés pour l'isolation entre chevrons, pour murs à isolation intérieure, extérieure, etc. ;
- la meilleure isolation pour se préserver des chaleurs estivales ;Polystyrène expansé, extrudé
Le polystyrène expansé est le principal
isolant d'origine synthétique. Il présente une structure à pores ouverts tandis
que le polystyrène extrudé a une structure à pores fermés lui assurant une
meilleure résistance à la compression. Tous deux sont imperméables et créent
une barrière étanche dans les murs, empêchant l'humidité du logement de
s'échapper par ce biais.
Sous l'action de la chaleur, le polystyrène
émet des styrènes et autres gaz toxiques contenus dans ses additifs ignifuges.
Il laisse constamment échapper du pentane pendant toute sa durée de vie.
Polyuréthane
Il est souvent employé sous forme de
mousses expansives pour calfeutrer les cadres de portes et de fenêtres. Il
libère des amines (substances dangereuses) et ses additifs ignifuges sont
également toxiques. Pour un prix élevé, cet isolant reste très efficace l'hiver
(meilleur coefficient ) mais relativement peu l'été.
Laines de verre ou de roche (rouleau,
plaques ou vrac)
Les isolants à base de fibres minérales
sont les plus répandus. La laine de verre est obtenue par fusion,
centrifugation et soufflage de verre de récupération tandis que la matière
première de la laine de roche est généralement du basalte. Leur pouvoir isolant
diminue fortement en présence d'humidité (d'où la présence de pare-vapeurs sur
les rouleaux).
Ces laines contiennent des fibres
respirables très irritantes pour le bricoleur qui est amené à les manipuler.
Depuis 1987, les laines minérales étaient classées 2B "pouvant être
cancérogènes pour l'homme" par le Centre International de Recherche sur le
Cancer.
En 2001, elles ont été reclassifiées dans le groupe 3 "ne pouvant être classées quant à leur cancérogénicité".
En 2001, elles ont été reclassifiées dans le groupe 3 "ne pouvant être classées quant à leur cancérogénicité".
Important : Il est important de noter que
sous l'appellation laine de verre ou laine de roche se classent des produits
d'une densité allant de 12 kg/m3 jusqu'à 130 kg/m3. Si
leur pouvoir isolant est sensiblement le même en hiver, les produits les plus
légers ne protègent absolument pas de la chaleur l'été. Comme à ce jour aucune
performance d'été n'est demandé aux isolants, il vous sera bien difficile
d'obtenir de votre revendeur ou poseur des informations sur le poids de
l'isolant qu'il compte vous fournir.
Chanvre en rouleau
Les fibres végétales sont une bonne
alternative aux laines minérales et présentent des qualités isolantes
équivalentes. Elles sont malheureusement absentes des grand circuits de
distribution. Les plantes telles que le chanvre peuvent être cultivées sans
engrais et leurs fibres sont naturellement fongicides et antibactériennes. Le
chanvre peut être utilisé en rouleau et en vrac comme la laine de verre (avec
des additifs ignifuges et anti-rongeurs tels que sels de bore ou d'amonium),
mais aussi pour être inclus dans des enduits ou bétons isolants entre solives.
Dans ce dernier type d'application avec un liant à base de chaux, le chanvre
n'a pas besoin d'additifs.
Cellulose
Généralement fabriqué à partir de journaux
recyclés, ce matériau a déjà conquis 25 à 30% du marché en Scandinavie et aux
Etats-Unis. Des additifs inoffensifs (sels de bore) le protègent contre
l'incendie, les insectes et la moisissure. Les flocons de cellulose sont
disponibles sous forme de panneaux ou en vrac. Attention : le caractère
écologique de ce matériau demeure contreversé. Si les particules de la
cellulose ne sont pas aussi fines que celles de la laine de verre, elles peuvent
néanmoins provoquer des inflammation pulmonaires lors de leur mise en œuvre en
l'absence d'une protection appropriée. De plus, il contient également les
résidus d'encre présentes avec le papier recyclé.
Perlite
La perlite est un isolant écologique fabriqué
à partir de roches volcaniques broyées et expansées thermiquement à plus de
1000°C: en s'évaporant l'eau fait gonfler les fines particules de roche qui
emmagasinent de l'air. La perlite est totalement inerte, ininflammable,
imputrescible, insensible à la vermine et aux rongeurs et totalement exempte de
toxicité. C'est le seul isolant pour combles perdus qui peut-être considéré
comme ayant des propriétés inaltérables dans le temps.
id+
- Quel que soit le mode d'isolation choisi, le fait d'utiliser une isolation renforcée permettra de diminuer votre consommation de chauffage, sa facture et les rejets associés.
- N'oubliez pas de juger votre isolant sur son efficacité en hiver et en été.
- Nous vous déconseillons les isolants en flocons pour les combles
- Nous vous déconseillons les isolants fibreux de trop faible densité (rouleaux ou flocons de moins de 40kg/m3) car ils se tassent progressivement et perdent en quelques années la majeure partie de leur efficacité. Pour cette même raison, évitez les produits « discount ».
- Si vous optez pour des matériaux naturels (ou plus généralement pour une construction qui sort du cadre des matériaux distribués largement), choisissez un professionnel spécialisé. Faire réaliser une prestation à un professionnel qui n'a pas l'habitude de manipuler les matériaux que vous exigez pourra conduire à un travail mal réalisé.
- Si vous optez pour des matériaux courants, optez pour le moins mauvais de ces isolants, à savoir la laine de verre ou de roche (pas de barrière étanche pour l'humidité, pas de libération de gaz douteux) et choissisez les de forte densité.
- Si vous êtes disponible, réalisez par vous-même l'isolation de votre maison. Vous pourrez ainsi réaliser un travail très soigné aux angles et aux entourages de fenêtres, ce qui permettra de limiter les ponts thermiques.
- Soyez cohérent dans votre choix d'isolation : il ne sert à rien d'avoir 20cm d'isolant sur les murs si vous utilisez des fenêtres standard, que vous ne respectez pas nos conseils sur la répartition des fenêtres ou que le coefficient de compacité de votre plan est mauvais.
Isolation phonique
En cas de zone extérieure bruyante, prévoir
des menuiseries extérieures à double vitrage 8/8/4 au lieu du standard 4/12/4
(chiffres indiquant respectivement l'épaisseur de la vitre extérieure, de la
lame d'air puis de la vitre intérieure). Toujours dans ce cas, préférez des
fenêtres ou porte-fenêtres ouvrant à la française aux baies vitrées. Vous pouvez
aussi demander des prises d'air extérieures (obligatoires) tapissées d'un
revêtement absorbant les bruits. De même, évitez les volets roulants avec
coffre en saillie côté intérieur.
Diminuer les bruits à l'intérieur de la
maison
- Prévoir des cloisons isolantes entre les parties jour et les parties nuit.
- Prendre des canalisations d'eau d'un bon diamètre.
- Utiliser un réducteur de pression.
- Eviter les appareils sanitaires adossés à une cloison d'une chambre.
- Choisir une chasse d'eau avec remplissage par tube plongeur.
Dans le cas de maisons mitoyennes, prévoir
si possible un mur mitoyen qui soit en réalité constitué de 2 murs, un pour
chaque maison, et séparés par une distance minimale de 1 cm . Si les murs se touchent,
les bruits d'impact seront aisément transmis d'une maison à l'autre.
![]() |
La
laine de bois
|
![]() | ||
Isolation de sol phonique avant
Isolation de sol phonique finie
|
![]() | ||
Démolition de cloisons
|
Posted by Batiment, On 14:10
Essai de Proctor
Laboratoire
Essai de Proctor
BUT :
L’essai Proctor a pour but de déterminer, pour un compactage d’intensité donnée, la teneur en eau à laquelle doit être compacté un sol pour obtenir la densité sèche maximum. La teneur en eau ainsi déterminée est appelée « teneur en eau optimum Proctor ».
PRINCIPE DE L’ESSAI :
L’essai Proctor consiste à compacter dans un moule standard, à l’aide d’une dame standard et selon un processus bien déterminé, un échantillon du sol à étudier et à déterminer le teneur en eau du sol et sa densité sèche après le compactage.
L’essai Proctor est répété plusieurs fois de suite sur des échantillons portés à des teneurs en eau croissantes (2%, 4% ,6% ,8% ,10%,12% ,14%,16%)On détermine ainsi plusieurs points de la courbe représentative des densités sèches en fonction des teneurs en eau. On trace alors la courbe en interpolant entre les points expérimentaux. Elle représente un maximum dont l’abscisse est « la teneur en eau optimum Proctor », et l’ordonnée « la densité sèche maximum Proctor ».
![]() |
Diagramme Proctor simple |
1. Essai Proctor normal :
Le compactage n’est que moyennement poussé. Il est généralement utilisé pour les études de remblais en terre (barrages et digues).
Il s’effectue en trois couches avec « la dame Proctor normal », l’énergie de compactage est de :
- 55 coups de dame par couche dans le moule C .B .R.
- 25 coups par couche dans le moule Proctor normal.
2. Proctor modifié :
Le compactage est beaucoup plus intense ; il correspond en principe au compactage maximum que l’on peut obtenir sur chantier avec les rouleaux à pieds de mouton ou les rouleaux à pneus lourds modernes. C’est ordinairement par l’essai Proctor modifié que l’on détermine les caractéristiques de compactage (teneur en eau optima, densité sèche maxima) des matériaux destinés à constituer la fondation ou le corps de chaussée des routes et des pistes d’aérodromes.
Le compactage dans ce cas-là s’effectue en cinq couches successives avec « la dame Proctor modifié » l’énergie de compactage est de :
- 55 coups de dame par couche dans le moule C.B.R.
- 25 coups par couche dans le moule Proctor.
APPAREILLAGE :
Il comprend :
1. Le moule Proctor constitué par un tube cylindrique métallique inoxydable de 10,15 cm de diamètre intérieur et 11,7 cm de hauteur, pourvu d’un fond et d’une hausse métallique amovibles.
2. La dame Proctor normal qui est constitué par un mouton de 2,49 kg (cylindrique de 5,1 cm de diamètre) dont la hauteur de chute est de 30,4 cm.
3. Du sable.
4. Une étuve.
5. Une règle à araser d’environs 250 mm.
6. Truelles pour le malaxage.
7. Des maillets, burins, couteaux, etc. pour le démoulage, ou mieux un appareil à démouler.
8. Une balance sensible au gramme d’une portée maxima au moins égale à 20 kg.
9. Une éprouvette graduée.
10. De l’eau.
11. Un bac.
![]() |
MATERIEL POUR L’ESSAI PROCTOR NORMAL |
MODE OPÉRATOIRE :
1. On prend 2,5 kg de sable préalablement préparé qu’on verse dans un bac.
2. On ajoute une certaine quantité d’eau (*) proportionnelle au poids du sable utilisé.
3. A l’aide de la truelle on malaxe bien le sable.
4. On remplit le moule Proctor normalisé en trois couches puis après avoir versé chaque couche on compacte l’aide de la dame Proctor normal en 25 coups en respectant la hauteur de chute et en assurant une répartition équitable des coups sur la surface à compacter. On procède de la même manière après la mise en place de la 2eme et 3eme couche.
5. Une fois le moule rempli, on arase le sable avec une règle à araser, on comble les vides laissés à la surface.
6. On prélève ensuite un échantillon d’environs 100 g à la surface du moule, puis on retire la base de ce dernier afin de prendre un 2eme échantillon d’à peu près du même poids.
7. A la balance, on évalue les masses des deux prélèvements puis on les fait passer à l’étuve au moins pendant 24h.au termes desquelles on va repeser les échantillons.
(*) : L’essai est répété plusieurs fois de suite sur des échantillons portés à des teneurs en eau croissantes (2%, 4% ,6% ,8% ,10%,12% ,14%,16%
CONCLUSION :
Sur les chantiers de stabilisation, on exige, en général, des densités sèches égales à 90 % ou à 95 % de la densité sèche maximum Déterminée à l’essai Proctor ; d’où l’importance d’avoir au moment du Compactage une teneur en eau très voisine de la teneur en eau optimum.
Cette Condition est souvent difficile à remplir, ce qui limite les possibilités de stabilisation des sols : en périodes de pluie, la teneur en eau du sol naturel est généralement supérieure à la teneur optimum, il faut aérer le sol pour le faire sécher ou attendre une période plus sèche. En période sèche les apports d’eau sont importants (la teneur en eau optimum varie entre 6 et 12% selon la nature du sol et l’engin de compactage utilisé.).
Posted by Batiment, On 13:27
Limites d'Atterberg
Laboratoire
Limites d'Atterberg
Sommaire |
|
Généralités
Les limites d'Atterberg sont des teneurs en eau caractéristiques des sols fins permettant entre autre d'établir leur classification et d'évaluer leur consistance. Ces valeurs de teneurs en eau permettent de caractériser également les différents états des sols : liquide, plastique, solide et solide sans retrait de ces matériaux. Cet un essai relativement long à réaliser (plus de deux jours en général et la durée[1] augmente avec la proportion d'argile). Bien que rudimentaire dans sa préparation, les résultats obtenus sont répétables et reproductibles.Les limites d'Atterberg comprennent :
- la limite de liquidité wL (NF P94-051[2] ou -052-1[3])
- la limite de plasticité wP (NF P904-051[2])
- la limite de retrait wR (XP P94-060-1[4])
Certains laboratoires utilisent la droite de Casagrande pour évaluer l'IP à partir de la limite de liquidité, que l'on retrouve dans un diagramme IP-wL. Cette droite a pour équation :
avec :
- 0,70 < a < 0,80
- 13 < b < 20
L'utilisation de cette formule est limitée à certains sols et doit faire référence à l'expérience régionale.
L'utilisation des limites est très intéressante pour évaluer les états hydriques des sols fins en terrassement. Pour cela on évalue l'indice de consistance du sol Ic. Plus la teneur en eau naturelle du sol se rapprochera de la limite de plasticité et meilleure sera sa consistance. En s'éloignant de la limite de plasticité, le matériau s'humidifie et sa consistance diminue. Il ne faut pas confondre la consistance et la plasticité. La position de la teneur en eau naturelle (wn)du matériau par rapport aux limites d'Atterberg permet d'exprimer cet indice de la façon suivante :
Description du mode opératoire
Ces essais se réalisent sur un mortier de sol composé de la fraction granulométrique 0/400 µm. Pour cela, l'échantillon homogénéisé de départ est au préalable humidifié dans un bac. La quantité de sol initial est environ de 200x le diamètre en mm des plus gros éléments (Dmax).Une fois le matériau ameubli il est tamisé sous eau au tamis de 400µm dans un bac de récupération suffisamment grand (photo 1).
Il faut ensuite laisser le mélange décanter pour éliminer l'excès d'eau (photo 2). Dès que l'eau devient claire, une première étape peut consister à siphonner l'excédent (photo 3). Pour réduire ensuite plus finement la quantité d'eau, un passage à l'étuve à des températures inférieures à 50°C peut être réalisé (photo 4). On peut également laisser évaporer doucement jusqu'à atteindre la teneur en eau la plus proche de la liquidité. Il convient d'être très vigilant afin de ne pas trop sécher le matériau car cela oblige à recommencer l'opération. Après séchage, le mortier est récupéré et malaxé sur une table en marbre pour homogénéiser autant que possible la pâte et éliminer les éventuelles boulettes qui auraient pu se former. Ce mélange doit être le plus lisse possible (photo 5).
Le mortier est enfin prêt pour commencer les essais.
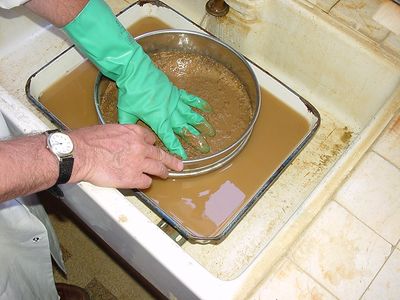

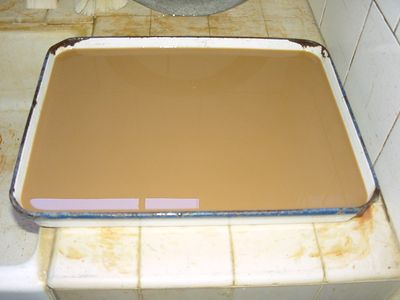

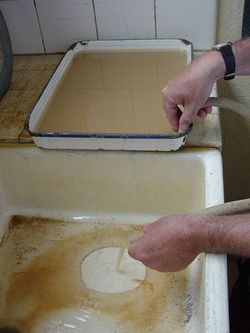

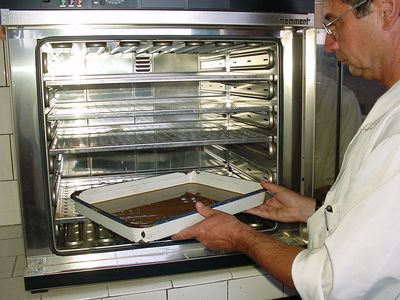

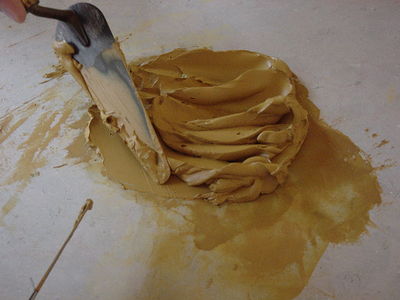

Les limites sont réalisées sur une plaque de marbre poreux ce qui aide à faire baisser doucement les teneurs en eau du matériau.
détermination de la limite de liquidité
- l'essai à la coupelle de Casagrande (NF P94-051[2])
- l'essai au cône de pénétration (NF P94-052-1[3])
détermination de la limite de plasticité
La limite de plasticité est définit par application de la norme NF 94-051[2] . Le matériau est roulé sous la forme d'un petit rouleau plein (ou boudin) d'environ 3 mm de diamètre. Ce boudin est progressivement asséché en frottant le matériau entre la plaque de marbre et un patin poreux (souvent en bois) (photo 6). Lorsque le rouleau n'est plus plastique, il devient alors cassant (photo 7). L'essai est arrêté car la teneur en eau à ce moment correspond à la limite de plasticité.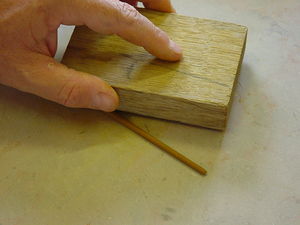

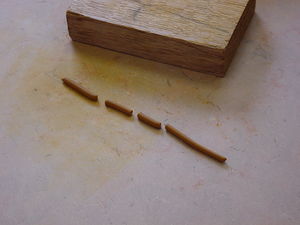

détermination de la limite de retrait

Utilisation des limites d'Atterberg dans le domaine routier
Les limites d'Atterberg sont utilisées pour identifier et classer les matériaux fins. Ainsi la norme NF P11-300[4] permet de distinguer différentes classes de sols selon les indices de plasticité des matériaux. Il s'agit même d'un essai à privilégier pour les sols fins au détriment de l'essai au Bleu de méthylène.Pour les matériaux très fins, contenant plus de 35% de passant à 80µm, on distinguera 4 classes de sols :
- les sols A1 dont l'IP est inférieur à 11 ;
- les sols A2 dont l'IP est compris entre 11 et 25 ;
- les sols A3 dont l'IP est compris entre 25 et 40 ;
- les sols A4 dont l'IP est supérieur à 40.
- les sables argileux B5 dont l'IP est inférieur à 12 ;
- les argiles sableuses B6 dont l'IP est supérieur à 12.
Incertitudes de l'essai
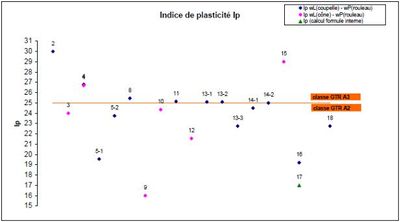

Disposer de la valeur de l'incertitude est important pour évaluer la portée du résultat. Cette information semble ainsi nécessaire pour valider l'application de résultats surtout lorsque l'incertitude affecte la conformité aux limites d'une spécification.
Incertitudes évaluées en 2011 sur la limite de liquidité à la coupelle
- limite de répétabilité : r = 3,7
- limite de reproductibilité : R = 7,0
- incertitude élargie pour k=2 : U = 5,0
Incertitudes évaluées en 2011 sur la limite de liquidité au cône
- limite de répétabilité : r = 1,7
- limite de reproductibilité : R = 8,0
- incertitude élargie pour k=2 : U = 5,7
Incertitudes évaluées en 2011 sur la limite de plasticité au rouleau
- limite de répétabilité : r = 2,9
- limite de reproductibilité : R = 7,7
- incertitude élargie pour k=2 : U = 5,4
Incertitudes sur l'indice de plasticité
L'indice de plasticité peut être obtenu indifféremment avec l'essai à la coupelle ou au cône. L'expression du résultat (voir graphique) montre au final une certaine dispersion par rapport à la moyenne.Posted by Batiment, On 22:57
Inscription à :
Articles (Atom)